Die produzierende Industrie ist ein Bereich, wo Erfassung, Auswertung und punktgenaue Verfügbarkeit von Daten entsprechend erfolgskritische Relevanz hat. Ein Beispiel für ein Digitalisierungsprojekt zur intelligenten Steuerung von Produktionsprozessen ist das Unternehmen Zoerkler Gears. Der burgenländische Familienbetrieb für innovative Antriebssysteme in Luftfahrt und Automobilindustrie beauftragte Kapsch BusinessCom mit der Integration intelligenter Sensorik in der Produktion.
Zielsetzung war ein sogenanntes Machine Manufacturing Execution Systems zur Unterstützung von Planung und Steuerung, wo ein digitales Abbild der Produktion die Überwachung der Abläufe und Maschinenparameter in Echtzeit ermöglicht.
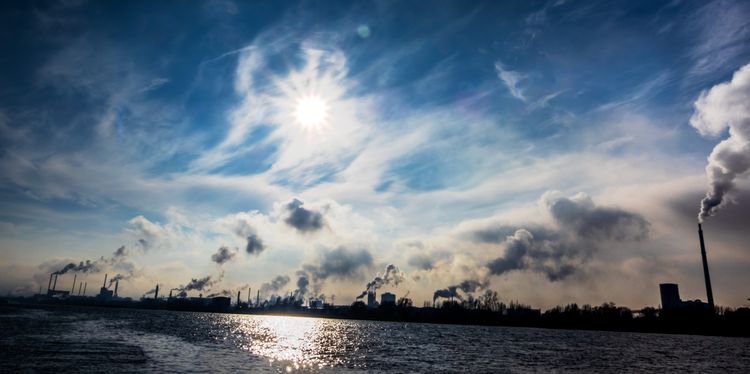
Der digitale Zwilling
Bei Zoerkler besteht durch die umfangreichen Fertigungstiefen ein heterogener Maschinenpark mit unterschiedlichen Kommunikationsstandards. Kapsch rüstete die Maschinen mit sensorbasierten IoT-Controllern aus, die auch indirekt in die Maschinensteuerungen eingebunden wurden und die Maschinendaten in Echtzeit an das Machine Execution System zur Aufbereitung weiterleiten.
"Speziell dieses Projekt zeigt, dass eine digitale Fabrik hohe Ansprüche an die IT-Infrastruktur stellt. Gerade die Produktionsdigitalisierung braucht aktuelle technische Standards und einen raschen Zugriff auf die hausinternen Ressourcen", so Markus Künstner, Experte für Manufacturing & Supply Chain bei Kapsch BusinessCom.
Das neue Manufacturing System ermöglicht nun die Erfassung exakter Produktionskennzahlen und Transparenz im Fertigungsprozess sowie ein Echtzeitmonitoring der Maschinenzustände und Auslastungen. Parallel wird eine automatisierte Wartung zur Reduktion etwaiger Maschinenausfälle gewährleistet. "Der wichtigste Aspekt bei so einem Projekt ist ein dynamisches und innovatives Projektteam, das sich mit den Themen Industrie 4.0 und Digitalisierung klar identifizieren kann", sagt Thomas Kranner, Project Manager bei Zoerkler Gears.
Breite IKT-Kompetenz
Ein weiteres Beispiel für die Digitalisierung von Produktionsprozessen ist das Unternehmen BHDT, Hersteller von Hochdruckkomponenten für die chemische Industrie. Bedingt durch einen gewachsenen, unterschiedlichen Maschinenpark konnten die Daten nicht einheitlich ausgelesen und verarbeitet werden. Um nun ein vergleichbares Bild von den Produktionsabläufen zu erhalten, wurde Kapsch BusinessCom als Generalunternehmer mit der Umsetzung dieses komplexen Daten- und Vernetzungsprojektes beauftragt.
Als ersten Schritt wurden alle Maschinen mit ihren Daten zentral vernetzt und plattformneutral aufbereitet und visualisiert. Mit dieser Vereinheitlichung kann die Produktion nun kontinuierlich optimiert werden und das inkludiert auch hier automatisierte Wartungen für eine höhere Verfügbarkeit der Anlagen. Die ebenso automatisierte Datenverarbeitung ermöglicht zudem lückenlose Qualitätsnachweise und eine Produktionsplanung in Echtzeit.
"Kapsch ist im Industrieumfeld bekannt für seine breite IKT-Kompetenz und hat rasch verstanden, welche Prozesse optimiert gehören und als Generalunternehmer eine durchgängige Lösung unterschiedlicher Technologiepartner und Systeme umgesetzt", so Andreas Weissenbacher von BHDT. (ecaustria)